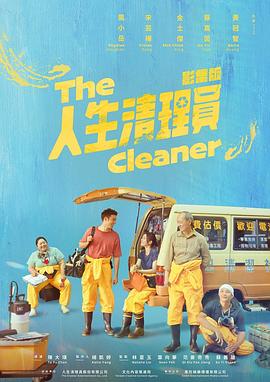
图片来源: 《祝你像姐一样》档案馆 - 清玉心 摄于 宁化县
本文由半导体产业纵横(ID:ICVIEWS)编译自semiengineering
热管、盖子、热界面和微通道冷却有助于消除芯片产生的热量。
半导体集成度的提高意味着需要在更小的空间内完成更多的工作,从而产生更多需要消散的热量。
管理先进节点芯片和多芯片组件的散热对其功能和寿命至关重要。虽然人们的注意力主要集中在提高功率效率以降低功耗增长率,但仅靠这一点还远远不够。
还需要各种技术来帮助热量向上、向下和向外移动。好消息是,我们在多个领域正在取得进展。
工作量越大,热量也就越多
电路工作所需的能量来自电源引脚,但并非所有能量都能转化为功。部分能量会以热量的形式浪费掉,必须将其从源头移除并排放到环境中。成功的设计必须平衡耗散率和能耗率。但除了功率之外,还需要考虑芯片内部热量来源的面积。面积越小,功率密度就越高,对改进冷却策略的需求也就越大。
Promex首席运营官戴夫·弗罗姆 (Dave Fromm) 表示:“关键在于设法从几平方厘米的面积中去除瓦特数的电力。单位面积的功率非常巨大。”
这也变得越来越成问题。“功率密度正在攀升,”安靠公司负责芯片/FCBGA集成的副总裁Mike Kelly说道。“铜混合键合等技术加剧了这一问题,因为3D堆叠的功率仍然集中在相同的x、y方向上。”
硅片的最大尺寸受限于用于构图的光罩(26 x 33 毫米),但封装却没有这样的上限。尺寸并非随意,部分原因是业界尚未大规模生产如此大的封装。生产线目前尚未配备相应的设备。然而,更大的封装会进一步散热,从而降低功率密度。
“我们并不是要把所有东西都放到一个固定的尺寸里,”凯利观察到。“尺寸在不断增大,这使得功率密度可能保持平稳,或者上升得更缓慢。这与硅芯片不同,硅芯片有刻线限制。”
然而,更大的封装尺寸可能更容易翘曲。“目前,60 x 60 平方毫米的封装尺寸很常见,”安靠公司 chiplet/FCBGA 开发高级总监 YoungDo Kweon 表示。“安靠公司也正在生产 85 x 85 平方毫米的封装尺寸。几年后,我们将生产出超过 100 x 100 平方毫米的封装尺寸。这意味着热应力可能会增加。”
材料的热导率以W/Km为单位。路径距离越短,热导率越高,因此路径上的任何东西越薄越好。
热量在封装中的传播方式
热量主要在有源硅层中产生。热量从那里向上移动,在倒装芯片封装中,这意味着热量会穿过体硅层到达封装背面,最终流出封装。热量还可以通过PCB 上各种金属连接向下移动,在某些情况下,热量甚至可能向侧面移动。具体移动方向取决于具体应用。
“如果你观察一下笔记本电脑之类的产品,就会发现它们的热量来自芯片背面和主板的另一面,”凯利说道。“但对于数据中心和高性能计算来说,穿过主板的散热路径阻力很大。所以95%以上的热量都是从顶部散发出去的。”
多年来,散热器(有些带有内置风扇)一直是高功率封装的标准配置。它们由铜或铝制成,金属材质的选择取决于散热器之后热量的流向。
铝的温度变化更快,因为它会吸收封装中的热量。更大的温度变化使热交换效率更高。“对于相同尺寸的散热器,改变铜的温度比改变铝的温度更困难,”Fromm指出。
如果散热器与空气交换热量,那么空气必然流动。空气的导热性很差。如果散热器与另一个导热固体连接,那么铜可能是更好的选择。铜的比热容更高,这意味着它可以储存更多的热量,而温度升高幅度不如铝。因此,铜与空气的换热效率较低,但如果连接到另一个固体上,它可以非常有效地将热量传导到后续的散热器中。
如果正在进行的计算工作具有突发性,且空闲时间较长,那么铜线也可以搭配风扇使用,因为它有更多时间与空气进行交换。“如果是短脉冲,且脉冲强度很高,且停机时间较长,那么铜线能够更好地随着时间的推移进行衰减,”Fromm 说。“铝线会瞬间变得非常热。”
热点芯片
热点带来了另一个挑战。与其让整个封装同时散发足够的热量来处理所有热点,不如使用散热器来平均分配封装内的热量。传统的金属散热器位于封装内部。它可以是一块独立的金属块,也可以是一个与芯片导热连接的金属外壳。
“实现良好散热的最佳方法是有效地沿垂直方向散热,”凯利说道。“如果你能非常有效地散热,热点就没有机会变得更热,从而将热量散发出去。”
连接散热片和其他元件的方法是一个正在积极开发的领域。它们被称为热界面材料(TIM),其作用是确保两个表面之间形成一个保形层。“最好使用胶水,但如果它不支撑部件,人们也会使用油脂,”Fromm 解释说。“关键在于消除气隙。理想的 TIM 材料能够保持原位,但从应力角度来看,它具有很好的保形性。”
典型的封装可能包含两个TIM,有时称为TIM I(罗马数字1)和TIM II。“封装内部有两个不同的接口,”Kweon说道。“一个位于[散热器]和[导热片]之间。另一个位于芯片背面[和导热片]之间。”
图1:热界面材料的两种典型应用。TIM I 位于芯片和散热器之间;TIM II 位于散热器(在本例中为外壳)和散热器之间。箭头表示散热方向。来源:Amkor
金属TIM即将问世
传统的TIM主要由聚合物制成。但由于聚合物导热性不佳,它们通常会掺杂导电添加剂。“人们正在用碳、石墨或各种高导热金属来掺杂它们,”Fromm说道。“金刚石是另一种人们开始使用的填料。金刚石的热活性可能比铜高5到10倍。”
即便如此,TIM 的导热性往往较差,因此保持其层数较薄有助于尽可能缩短热路径。它们对于散热功率约为 100 W 的封装来说已经足够好,但预计新型芯片和先进封装的散热功率将超过 1,000 W,这将对现有材料构成挑战。
如今,金属TIM(尤其是铟合金)的热导率大幅提升。Amkor公司发现,改用铟合金可以将芯片结温降低10°C以上。“(使用聚合物TIM)温度升高10°C通常意味着芯片寿命缩短一半,”Kweon指出。“现在很多客户都希望(用于功率高于400W的芯片)采用金属TIM。”
图2:采用金属TIM的模压FCBGA。来源:Amkor
TIM受热膨胀的速度与其附着材料不同,因此粘合剂可能比润滑脂承受更大的热应力。对于Kweon预见到的几年后出现的更大尺寸封装来说,这可能是一个问题。“这意味着,如果你使用聚合物TIM,它可能无法很好地工作,因为芯片边缘周围的拉伸应力可能导致分层,”他说。
系统侧组件
流动空气所能提供的冷却效果有限,因此,对于更具挑战性的组件,液体的使用方式多种多样。用液体(浸没式)包裹封装或子系统比用空气更有效地散热。
“到了一定程度,当功耗达到 800 到 1200 瓦时,根据封装结构的不同,风冷系统就无法再维持了,”Kelly 说,“你必须采用某种液冷技术,让冷却液直接与芯片接触,从而提供低温。”
这需要一个封闭的系统,液体可以在其中从发热组件循环到交换器,该交换器可以冷却液体,然后再返回到封闭的循环中。这还会提高芯片和冷却液之间的温度梯度。“这会导致各处的应力都更高,”凯利指出。“好消息是,现在的IC封装材料比10年前好多了。”
传统的液冷技术完全依赖于液体,但更先进的技术则结合了液相和气相。“最先进的冷却方法是两相沸腾流,”新思科技高级工程师Satya Karimajji 表示。
浸没式冷却技术将液体冷却技术更进一步,将整个系统浸入流动的液体中,其散热效率远高于其他技术。然而,这种方法复杂且成本高昂,因为系统必须密封以容纳液体。研究的重点是寻找最有效的液体。“他们正在研究可以使用的不同类型的介电流体和制冷剂,”卡里马吉说。
当空间有限时
液体/气体散热也有两种不同的方案。均热板虽然并非新技术,但作为一种散热方式正变得越来越流行。“如今,许多客户正在转向在封装顶部加装冷却板的均热板,”Kweon说道。
均热板并非采用金属块,而是采用密封腔体,腔体内的蒸汽一侧与芯片接触,另一侧则设有冷却板。均热板属于两相系统,热源侧充当蒸发器,冷源侧充当冷凝器。均热板内部通常含有某种芯吸材料,有助于将冷凝液带回蒸发器。
“假设热量在一个很小的区域内消散,但你想将热量扩散到更大的区域,”Karimajji 说。“(均热板)可以增强散热器底座的温度均匀性。”
对于笔记本电脑和手机等缺乏散热器空间的系统,热管可以将热量从热源处进一步转移。冷凝的液体将通过毛细作用移动到蒸发器,并将蒸汽推向另一侧。产生的热量驱动系统运转。
“比如说,在笔记本电脑里,你没有足够的空间(在CPU附近)加个风扇,”卡里马吉说。“他们会用一根热管从CPU顶部一直延伸到笔记本电脑的边缘,然后把风扇放在那里。这样做的好处是不需要泵了。”
尽管冷却能力一般,但最大的优势在于热管的尺寸。“单靠热管本身可能不足以冷却GPU,”Karimajji指出。这些结构中使用的液体通常是去离子水,但根据工作温度,也可以使用制冷剂。
加盖或不加盖
封装上的盖子为封装内容物提供保护和机械稳定性。但裸露芯片背面则为不同的冷却技术打开了大门。
“盖子有助于散热,从而提升整体热性能,”Kelly 说道。“此外,在测试过程中配备保护结构也大有裨益,因为功能性或系统级测试的插入在机械上非常严格。因此,拥有盖子的客户非常乐意使用。如果没有盖子,他们在测试过程中总是会非常注意机械完整性。”
正在开发的冷却技术之一是水冲击,即将水喷洒在暴露的无盖芯片的背面。
“如果你直接把水喷到硅片顶部,就能比用某种水套来散热多得多,”凯利说。“水不会发生相变,但硅片旁边的水边界层会变得非常薄,因此热阻非常低。”
对于没有盖子机械支撑的芯片,放置在基板边缘的环等加强筋可以帮助提供刚性并减轻温度变化时的翘曲。
更奇特的是微流体技术,它涉及内部微通道,冷却剂可以通过这些微通道流动。液体并非简单地环绕封装,而是流经这些通道,在内部吸收热量。
“微型散热器由两部分组成,一部分位于CPU模块顶部,另一部分带有一个带风扇的散热器,”Karimajji说道。“它们之间有一个液体回路连接。液体流经CPU模块,吸收热量,然后流向冷却液储存器(称为散热器),散热器就位于此处。它将热量交换回环境,然后冷液体被泵回CPU模块。”
这对于硅片堆叠的冷却尤其有前景。堆叠顶部的硅片很容易将热量散失到环境中,而中间的硅片则必须以某种方式将热量排出堆叠。微通道现在为中间的硅片提供了一种更有效的散热方式。但代价是复杂性和成本。
目前,这些系统主要都是单相系统。“业界正在努力将双相[系统]从研究阶段推进到商业化阶段,”卡里马吉补充道。
将热量向下传导至PCB
热量向下传导至PCB并最终传导至系统其他部分的路径更为复杂。热量流动的自然路径是通过芯片与基板之间的界面(即芯片贴装层)以及从芯片向下传导至PCB连接点的金属引线。
在先进的封装中,并非所有引线都延伸到封装外部。这些内部信号会在封装内的组件之间传递热量。而那些延伸到外部的信号可能需要穿过中介层或硅桥才能到达基板。
“我们的中介层最多可以有六层,”Karimajji 说道。“但如果这还不够,那么从封装顶部散热也是一条平行路径。”
导热性更好的共晶合金可以改善芯片粘接处的热传递。引线也发挥了一定作用。
Fromm 表示:“金属密度有助于散热。接地连接和平面对此很有帮助。但是,如果芯片的高互连区域确实产生了热量,那么它就是净热源,而不是散热片。”
Synopsys 产品管理总监 Keith Lanier 表示:“裸片的最高温度取决于互连凸块的密度。使用 EDA 优化工具,你可以改变凸块密度,从而影响裸片的最高温度。”
新型焊料和基材
焊料的类型也很重要。金锡焊料在这方面表现良好。“标准焊料的功率密度约为 20 至 30 W/mK,”Fromm 说道。“金锡焊料的功率密度约为 60 W/mK,比标准焊料高出三倍。”
烧结银也受到了一些关注,尤其是在功率器件领域。“有一类材料是糊状的。它们像环氧树脂一样被分配,”Fromm说。“烧结后,它们的热导率非常高——70到100或150 W/mK。”
据Kweon 介绍,Amkor 也在研究铜铅键合技术,但铜铅键合材料更具挑战性,需要更精细的加工,从而增加了成本。Fromm 表示:“虽然可以做到,但表面必须非常清洁,而且必须控制表面氧化,所以必须在惰性气体环境下进行。” 这些挑战与铜基混合芯片间键合的挑战如出一辙。
所有这些潜在的热路径,无论是通过引线还是芯片贴装,都会穿过基板,然后到达PCB。标准有机基板的导热性适中,但未来可能会出现导热系数更高的陶瓷基板。
弗罗姆说:“在我看来,最理想的状态是高密度、高导热性的陶瓷,它可以吸收热量并提供足够的 I/O 密度。”
这种基板比有机基板更贵,但它们也比有机基板更平整、更坚硬,从而可以提高生产良率。“也许组装良率会推动基板成本更高的经济效益,”Fromm若有所思地说道,“如果我能以更高的良率制造它,或者获得更高的性能,那或许就值得了。”
将热量转移到芯片侧面
将热量从芯片侧面移出,可以增加一条散热路径来帮助芯片冷却。虽然单个芯片可能太薄,因此这种散热路径效果不佳,但堆叠芯片可以从侧面散热路径中受益,因为这样可以避免微流体技术的成本和复杂性。其中一种方法是模塑倒装芯片球栅阵列(FCBGA)。
在标准FCBGA封装中,元件周围有空气。而模塑FCBGA封装中,空气空间则填充了导热模塑化合物,使热量能够从堆叠芯片的侧面散发出去。
Kweon 表示:“对于芯片堆叠而言,夹层芯片缺乏良好的散热路径,因为芯片周围(封装内部)的空气导热性非常差。” 模塑材料取代了空气,改善了侧面的散热路径。
对于应力更大的先进硅节点来说,这一点可能变得更加重要。“(硅工艺)很快就会达到2纳米,”Kweon补充道。“在这种情况下,层间电介质非常脆。模塑FCBGA可以降低热应力屏障。”
图3:模塑FCBGA封装。模塑材料取代了封装中的空气,改善了侧面的散热路径。来源:Bryon Moyer/半导体工程
如此多的选择
随着芯片和封装产生的热量越来越多,冷却方案的数量也在不断增加。考虑到封装内元件之间的相互作用,组装方式的变化往往是渐进式的。即使即将出现革命性的新系统,也不太可能取代我们现有的系统。因此,我们在这里看到的这些零碎部件将以不同的组合方式持续演进。
尽早开始设计至关重要。“我们确实看到前期工作量很大,包括架构探索,甚至在 RTL 级别,”新思科技 SoC 工程高级总监 Shawn Nikoukary 表示。“我们必须影响芯片的架构,才能获得最佳的热性能。我们在架构阶段做的工作越多,最终就越容易。”
重要的是不要忽视应用所规定的成本上限。“数据中心人员往往会有一些相当独特的解决方案,”凯利指出。“他们所在的市场更容易负担得起这些方案。但如果考虑笔记本电脑、台式机或其他边缘设备,我们真的必须关注成本和高效散热。”
*声明:本文系原作者创作。文章内容系其个人观点,我方转载仅为分享与讨论,不代表我方赞成或认同,如有异议,请联系后台。